Warehouses are dynamic environments with numerous moving parts and potential dangers. A Risk Assessment allows you to review these hazards in your workplace and proactively mitigate them to keep your team safe.
In this article, we explain how to conduct an effective workplace Risk Assessment and share our recommendations for controlling traffic risks and implementing changes.
What is a Risk Assessment?
A Risk Assessment considers the likelihood and potential consequences of a hazard. This can help you determine the risk's severity and analyse the efficacy of any existing control measures. Based on these findings, you can identify what action you should take to control the risk and how urgently the action needs to be taken.
The extent of a Risk Assessment can vary depending on the type of hazard and available resources. In some cases, it may involve a simple discussion with your employees while in others it may require processes and techniques recommended by safety professionals.
When to conduct a Risk Assessment
Health and safety risks in the workplace should be regularly reassessed, particularly when operations change. This is ongoing, allowing you to flag any new hazards and processes requiring extra attention.
Examples of when to undertake a Risk Assessment include:
- Workplace incidents occur.
- Work practices and environments change.
- Demand fluctuates.
- Resourcing is adjusted.
- Workers are reintroduced into the workplace following stand-down arrangements.
- Workers or health and safety representatives raise concerns.
What is change management?
Before implementing new procedures or making changes at your workplace, the systematic process of change management should be employed to identify risks associated with a planned change. Companies must ensure that staff are notified in advance. These changes may range from the introduction of new mobile plant to new materials like concrete flooring or chemicals used in the warehouse. This allows employees to adapt accordingly and therefore can prevent incidents or injuries
When a Risk Assessment highlights a health and safety risk, it is tempting to take immediate action. However, rushing this process may raise new issues as a result. The change management process will allow you to predict any potential challenges in advance and prepare for them accordingly. As a result, your new processes will be safer and more effective.
Workplace risk management
Some of the common hazards in workplaces involve vehicles and traffic management.
If vehicles and pedestrians share the same workspace or route, there is a constant risk of injury and even death.
A Site Safety Audit assesses the safety of your warehouse, with particular attention to:
- Workplace layout
- Traffic demand
- Traffic prioritisation and control
- Pedestrian and vehicle traffic routes
- Requirements for special vehicles
- Emergency services access
- Lighting and visibility
- Speed limits
- Parking requirements
- Safe access to facilities for visitors or customers
A Site Safety Audit allows you to implement an effective Traffic Management Plan and ensure a safer environment for staff and visitors. This is achieved by providing clear expectations of site regulations and taking steps to separate pedestrians from equipment.
How to control traffic and mitigate risks in your workplace
According to the Safe Work Australia Traffic Management Guide, an organisation must eliminate traffic hazards from the workplace where it is reasonably practicable. If a risk cannot be eliminated, the organisation must take reasonable steps to minimise it.
The Hierarchy of Control outlines the order of steps for PCBUs to take, from the highest level of protection to the lowest.
- Elimination — Firstly, PCBUs must aim to eliminate the risk.
- Minimisation — If elimination is not feasible, the risk should be minimised by substituting the hazard with a safer alternative, isolating the hazard, and/or using engineering control measures.
- Administrative controls — If risk remains, administrative controls of vehicle operations should also be implemented to control traffic operations and pedestrian access.
- Personal Protective Equipment (PPE) — In addition to the above measures, personal protective equipment should be worn, such as high-visibility clothing.
Hierarchy of Controls
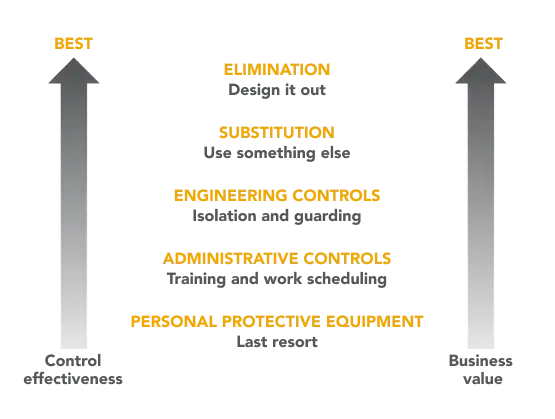
Recommended warehouse traffic controls
If traffic-related risks cannot be eliminated on your work site, we recommend incorporating the following control measures:
Pedestrian controls
You can reduce the risk of pedestrian-vehicle collisions by implementing barricades, safety zones, designated walkways, or safety railings. For pedestrians working with vehicles, install clear warning signs and enforce wearing high-visibility clothing at all times.
Load-shifting equipment
To minimise risks with loading, the most effective option is to use low-speed, stable, and lightweight load-shifting equipment. Where forklifts are used, the best way to minimise the risk of forklift-related injuries is to separate pedestrians and forklifts.
If separation is not possible, consider changing the layout of the work area, installing high-impact safety barriers, enforcing speed limits, using speed-limiting devices, or implementing pedestrian exclusion zones.
Workspace layout
When it comes to your workspace layout, consider minimising the cross-flow of traffic, intersections, and eliminating blind spots. You can minimise risks by using line markings in relation to traffic flow, driver-designated safety zones, pedestrian exclusion zones, parking areas, and speed limits.
Visibility and signage
To ensure all workers and pedestrians can operate safely within the space, you must maximise visibility. Effective control measures include installing mirrors, reversing cameras, sensors, or alarms to help drivers as well as pedestrians install visual warning devices like flashing lights and high-visibility markings.
Additional measures may include appointing a trained traffic controller to direct vehicle movement and ensuring high-visibility clothing is worn.
The SafeQuip Site Safety Process
At SafeQuip, our team will guide you through every step of the process, as follows:
1. Initial Site Safety Audit
The first step is the Safety Audit process, in which our experts will visit your site and interview key stakeholders to identify any potential hazards. Based on a robust Risk Assessment system, we will consider workplace layout, traffic volumes, traffic prioritisation, traffic routes, pedestrian and vehicle separation, signage, lighting and visibility, and speed limits.
2. Developing safety documentation
Based on the audit results, we will develop an effective plan to ensure your workplace meets all safety standards and regulations. This plan will include a complete set of safety documentation, including the following:
Risk Assessment
Following a Site Safety Audit, we create a Risk Assessment, which considers the likelihood and potential consequences of a hazard, guiding necessary actions and their urgency. The extent of a Risk Assessment can vary depending on the type of hazard and available resources, ranging from employee discussions to professional processes.
Traffic Management Plan
The next step is developing a Traffic Management Plan, which outlines designated pathways, vehicle operation zones, and safety protocols, ensuring the safety of both employees and visitors. Implementing a comprehensive Traffic Management Plan is essential to ensure a safe and productive worksite.
Traffic Controls map
We then develop site maps to display traffic controls in line with traffic management standards. These maps can be displayed on conditions of entry signage, training manuals, and safety notice boards to educate relevant audiences.
Traffic Management Standards Manual
For larger multi-location clients, we then create a Traffic Management Standards Manual detailing your company's traffic management protocols across all sites. This includes standards for signage, line marking, barriers, etc that ensure each site manager adheres to company standards.
All documentation will be subject to the Hierarchy of Control, ensuring the most advantageous balance of business value and control effectiveness.
3. Project implementation
Our project management capabilities allow us to combine multiple projects into one simple package. Depending on your needs, this may include signage, line-marking, concrete sealing, wheel stops, bollards and barriers.
We also offer an installation service where our team will install your purchase safely and efficiently. For best results, we strongly recommend that our professionals install certain products. Delivery or installation will be organised at a time that is the least disruptive to your organisation.
Our install team are continually trained to be compliant to the latest legislation. This includes WH&S legislation, height safety regulations and Current Codes of Practice. We also maintain relevant insurance, compensation and code compliance.
Summary
In conclusion, a Risk Assessment will identify the likelihood and consequences of a hazard in your workplace. Based on the assessment, you can develop documentation and implement changes that will control these risks. When risks are identified, change management anticipates challenges and ensures that new processes are safer and more effective.
Effective risk management in your workplace will not only enhance your team’s safety but will also contribute to operational efficiency. If you are interested in conducting a Risk Assessment of your workplace, download our free Risk Assessment Template - designed to help you identify high-end risks. Alternatively, contact our team of experts today to discuss your requirements.