What would a warehouse or site accident cost your company?
Over the past decade, over 1,880 traumatic injury fatalities have occurred in Australian workplaces. What’s more, over 1,165,100 employees have made a compensation claim for a workplace injury, each resulting in at least one week of working time lost.
A worksite injury will bring your operations to a halt and may cost your company both in lost revenue and productivity. Fortunately, in most cases, the implementation of effective site safety processes can prevent such accidents from occurring.
In this article, we cover the risks of neglecting worksite safety and offer practical advice on how you can improve the safety procedures on your site.
What is site safety?
Site safety refers to the general rules and procedures that must be enforced to protect people on your worksite. This ranges from wearing personal protective equipment (PPE), using the appropriate equipment, or following correct reporting procedures. Key components of site safety include:
Emergency Response Plans
An Emergency Response Plan prepares and directs your staff for various scenarios, such as a natural disaster or fire. It is important to develop thorough Emergency Plans in advance, ensuring everyone knows what to do if the need arises.
Traffic Management Plans
A Traffic Management Plan outlines the flow of people and vehicles around your worksite, ensuring hazards are identified and removed. Traffic Management Plans are essential in high-traffic environments to minimise collisions and other safety risks.
Inspections
Regular inspections allow you and your team to identify problems and maintain the safety of the workplace. For example, you may note that some equipment needs to be replaced or the safety signage needs to be updated. Remember, this shouldn’t be a one-and-done situation – inspections should be conducted regularly.
Equipment and vehicle servicing
Maintaining workplace equipment ensures it operates as safely and efficiently as possible. By conducting regular services on every machine, you can greatly reduce the risk of related accidents.
The consequences of poor site safety
Economic loss
Safe Work’s research shows that, in the absence of work-related injuries and illnesses, the Australian economy would grow by an average of $28.6 billion annually.
Lost Time Injury (LTI)
When a worker is injured on the job and cannot perform work duties for a day or more, it is recorded as a Lost Time Injury (LTI). They may need their work duties to be modified during recovery or, in some cases, may not be able to return to work at all. This will not only impact the worker on a personal level but also the company and other staff.
Potential for legal issues
In addition to loss of revenue and productivity, workplace injuries may lead to the company being subjected to legal action. These lawsuits can be extremely costly and time-consuming, and in many cases, can severely damage a company’s reputation and future.
Workplace hazards
Some industries are more susceptible to workplace hazards and safety challenges than others. In 2023, the highest worker fatality rates were in the transport and warehousing industry, closely followed by construction and forestry.
This is no surprise, given that 42% of the year’s fatalities were vehicle incidents, followed by falls from a height which accounted for 15%. In these injury-prone industries, workers are frequently exposed to hazards, increasing the risk of an accident.
In particular, workplaces with moving machinery or vehicles are some of the most at risk, accounting for 42% of fatalities in 2023. With this in mind, it is worth developing a Traffic Management Plan for your worksite and booking a Site Safety Audit.
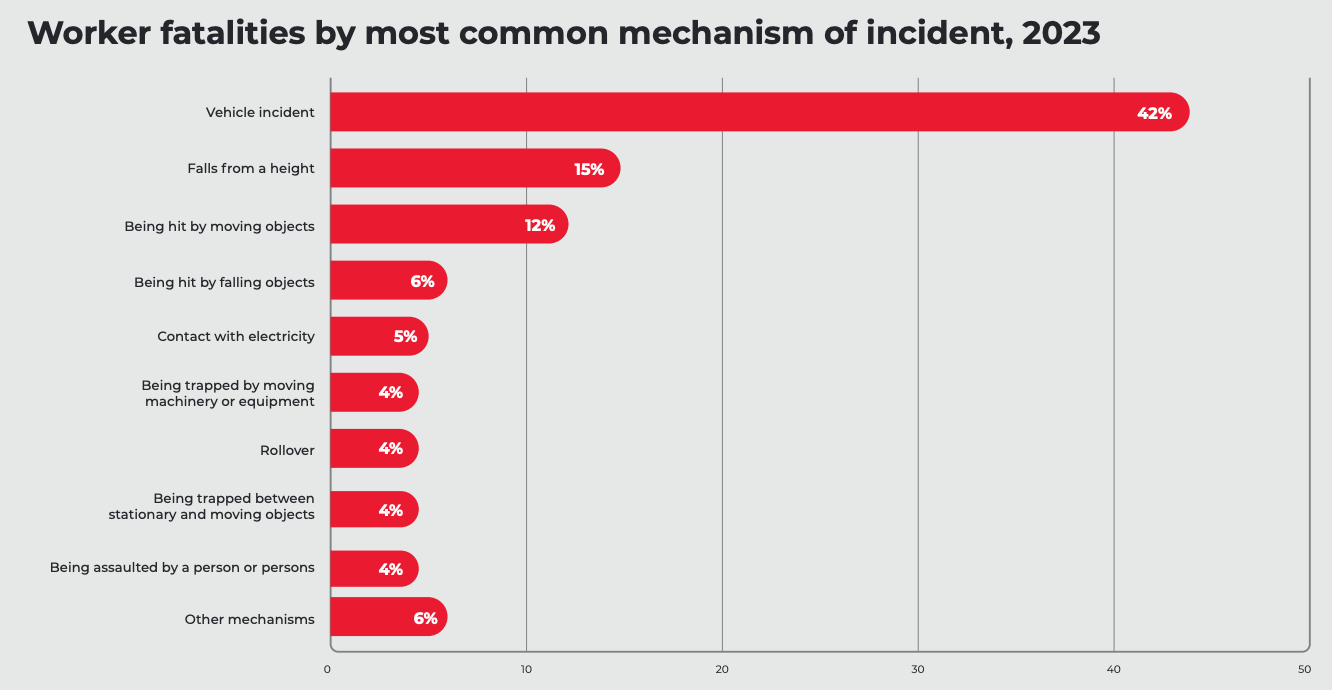
Source: SafeWork Key Work Health and Safety Statistics Australia 2024 report
What is a site safety audit?
A Site Safety Audit assesses the safety of your worksite, including any movement, loading, unloading, parking, and pedestrian access throughout the facility. It considers the following:
- Workplace layout
- Traffic demand, prioritisation, and control
- Pedestrian and vehicle routes
- Signage
- Requirements for special vehicles
- Emergency services access
- Lighting and visibility
- Speed limits
- Parking requirements
- Access for visitors or customers
Conducting site safety audits
At SafeQuip, we follow three key steps in our Site Safety Audit process. These steps are as follows:
Site Audit
Our experts will visit your site and interview stakeholders to identify potential hazards. Based on our risk assessment system, we’ll analyse the layout, traffic, main routes, pedestrian pathways, signage, visibility, speed limits, and more.
Safety documentation
We will then develop a plan to make sure your workplace fulfils safety standards. This will include a set of safety documentation, including a Risk Assessment, Traffic Management Plan, Traffic Controls Map, and Traffic Management Standards Manual.
Implementation
Depending on your needs, we will install the appropriate safety measures for your company, which can include safety signage, line marking, concrete sealing, wheel stops, bollards, and barriers.
If you want to assess your site safety, our Site Safety Quiz is a great place to start. Simply answer a few questions and the tool will tell you the most beneficial next steps. Alternatively, reach out to our team of experts to discuss your needs and we’d be happy to help.